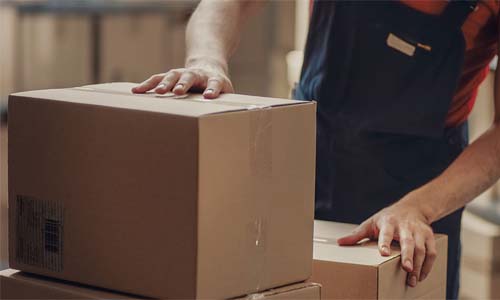
Strength is the most important quality characteristic for packaging board: the packaging needs to be strong and stiff enough to endure the strains of transport and protect the product inside. While the use of recycled fibers as raw material in packaging grades continues to increase, the board producers are facing challenges in meeting the strength targets. Why dry strength is a major challenge in recycled board production?
“Many packaging mills that produce recycled containerboard are facing challenges in achieving the desired strength targets for their products,” recognizes Vladimir Grigoriev, Senior Manager, Applications & Marketing, Pulp & Paper at Kemira.
Dry strength of board is an important functional requirement and there is an increasing demand for high performance grades in the packaging value chain. At the same time, the use of recycled fibers as raw material increases.
“The issue is that maintaining and improving strength properties in recycled packaging grades cost-effectively with the available means is a challenging task. And this is especially true in Europe.”
Here are 3 key reasons why dry strength is a challenge in recycled board production.
Deteriorating recycled fiber quality
The first challenge for strength is the availability of high-quality recycled fiber raw materials. The quality of the furnish has a direct impact on the board producers’ ability to build mechanical strength in the recycled board.
“This is a major challenge in recycled board production in Europe today, and the downward trend of recycled fiber quality is starting to be visible in other regions as well. There are less virgin fiber materials coming into the recycling process e.g. due to the decreasing consumption of printing and writing papers, and together with the increasing number of cycles in the fiber recycling, the raw material quality deteriorates,” says Mikko Virtanen, Senior Specialist, Applications & Marketing, Pulp & Paper at Kemira.
To compensate for the weaker fibers, the recycled board producers are forced to add higher quality fibers to their furnish, maintain extra sheet grammage or use more strength aids such as starch. This can quickly add to the production cost, hurting profitability and competitiveness in the market.
In many cases, the use of starch as a dry strength additive is already at a limit and increasing the dosage is neither effective nor economical.
“In many cases, the use of starch as a dry strength additive is already at a limit and increasing the dosage is neither effective nor economical. Starch slows down sheet dewatering, which leads to a decrease in machine productivity or an increase in energy consumption.”
Difficult and demanding process conditions
The second major challenge in the recycled board production are the demanding wet end conditions at a board machine. The mills often operate with largely closed water loops, recirculating and reusing the process water. As a result, the colloidal and mineral contaminants that come from recycled fibers accumulate in the water loop, negatively impacting the process conditions.
“When recycled fibers are used in paper production, it leads to higher conductivity and increased ash levels in the process water. These conditions damage the effectiveness of traditional dry strength chemicals, and again, in Europe the situation is far more challenging than in other regions.”
“In Europe, the recycled fibers often contain 15–20% of mineral filler and the fresh water consumption can easily be as low as three cubic meters per ton of paper, which can lead to conductivity of up to 7mS/cm. No wonder the traditional dry strength additives lose their efficiency,” explains Vladimir Grigoriev.
Need to reduce the packaging weight
The demand for sustainability in the packaging value chain puts focus on lighter weight packaging materials. The requirement for reducing the unit weight while maintaining high protection functionality is another challenge for dry strength in the recycled packaging grades.
“In recycled containerboard production, lightweighting is currently not as high on the agenda as it is for some of the other grades, e.g. cartonboard. But in the long run, the overall trend will increasingly impact also the recycled packaging materials. These grades are typically the ones that are used in secondary packaging when shipping goods around the world, so reduced grammage and lower weight also support the overall reduction of fuel consumption and CO2 emissions,” points out Grigoriev.
Currently, it is not uncommon that recycled board producers resort to overweighing in order to achieve the needed dry strength. The thicker the board, the better the strength properties.
“Maintaining the strength properties with reduced basis weight enables both economical and ecological benefits. The overweighing is not the most cost-effective way to solve the problem,” states Virtanen.
Unique strength polymer for recycled grades
To overcome these specific challenges in recycled board production, Kemira is introducing a new strength polymer for recycled furnish. Due to its unique polymer structure, FennoBond 6400 enables improved strength performance even in the demanding process conditions.
“With the help of effective dry strength chemicals, the recycled containerboard producers can have the needed flexibility to adjust their production to the varying raw material quality while ensuring that both the productivity targets and the required functionality of recycled packaging board grades are met.”