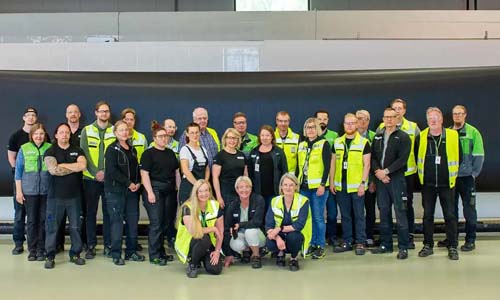
When it comes to quality, Valmet’s Black Belts have inevitably reached the world’s number one position. Do you want to know what is the secret behind the success? The truth is, there is no secret, but dedication and hard work.
Valmet has manufactured belts for shoe presses for almost 30 years. Today, we offer a comprehensive collection of belts with different reinforcing structures and surface options to fulfill the demands of each shoe press position in board, paper, tissue and pulp mills.
In addition to their unique characteristics designed to fit the customers’ needs, Valmet’s belts are known for their high quality – excellent wear resistance, efficient dewatering properties, chemical and heat resistance, and long lifetime.
Data-driven product development
We have a very systematic approach to product development and problem-solving. We strive to continuously improve the small details contributing to the overall quality of our belts. We are to a great extent utilizing data in all we do, and together with a team consisting of young talents and experienced experts, I think they make a winning combination,” says Lasse Janhunen, Product Manager at Valmet.
Our belt scanner is already a classic, as we’ve utilized it to monitor belts over their lifecycle from production to removal for over 20 years already. We also have a unique test machine in our in-house laboratory, giving us the opportunity to examine how belts retain their properties under extreme nip loads – an important asset when introducing new products to the market or examining the used belts after their removal,” explains Janne Honkanen, Product Manager at Valmet.
Valmet values the continuous co-operation with its customers
Today, many paper-makers appreciate the belt’s contribution to increased dry content after the press section and the energy savings it generates, thus want to optimize the belt’s water removal capacity, and go for a belt change already when it is still in decent condition. Others value the belt’s lifetime over its flawless performance, and it isn’t the least uncommon to see running times of over two years for our belts. Whatever the case, our goal is to always find a solution that best supports the customer’s targets – and I’m proud to say we succeed in it very well,” Lasse Janhunen says.