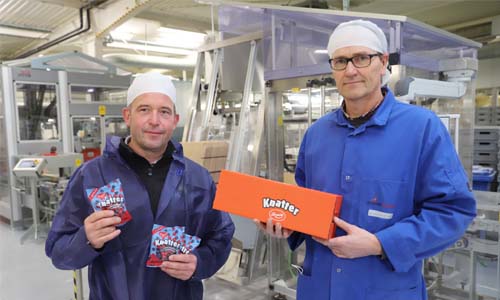
Seigmenn, Knatter, Minimix and other types of candy are fed into one end of Brynild’s new production line and come pre-packaged in bags and stacked in boxes on pallets at the other end. The fully automatic packing machine and pallet loader are supplied by VPK PackTech in Sarpsborg, which outperformed providers throughout Europe.
“PackTech delivered according to all our specified requirements, and was the best choice regarding a number of important parameters. In addition, it is great to have a supplier who can be here in 20 minutes if we need assistance,” says Brynild’s project manager and project engineer Viggo Ersøybakk.
VPK PackTech is part of VPK Packaging Nordic. With more than 35 years of experience and more than 900 installations and upgrades across Scandinavia, they specialize in reliable and efficient solutions for their customers. VPK has factories throughout Europe, and can offer products and solutions to the entire value chain. Ranging from the development, design and production of packaging to complete, tailor-made packaging lines.
A packing line of precision engineering
The whole packaging line that was delivered to the nut and candy manufacturer in Fredrikstad consists of a fully automatic wrap-around packing machine from Österbergs Förpackningsmaskiner AB, pallet elastics from Intersystem AB and transport system from Carryline AB. A packing line is a long line of advanced interactions between electronics and mechanics, fine-tuned down to millimetre precision.
VPK’s installations are in action after the products are placed in bags and checked on the production line. From there, they are transported into the packaging machine, which shapes and glues a corrugated board around the correct number of products. The packaging also labelled before it continues its journey towards being palletised. Boxes with any deviations are removed from the line.
In the palletizing machine, the boxes are pushed into place on pallets and come pre-stacked – ready to be transported onwards towards the warehouse or retailer – and then on to the consumer for a sweet treat.
“We sent out requests to 8-10 suppliers at home and abroad with our requirements and needs for speed, box sizes, layout plan etc., and were left with three of them in a final round.”
“The machines were also physically smaller than the competitors’ offering, which made it easier to install in the production hall. VPK could also deliver on time even during the difficult times of the pandemic and kept to the schedule”. Ersøybakk adds: “It would have been far more complicated if we had chosen a supplier from Germany, as the installers would have had to been quarantined every time they came to the country.”Fast delivery timeVPK PackTech’s project engineer and salesman Lars Hansen is pleased that they can contribute to increasing value for Brynild, and have a history of providing Österbergs machines at company’s candy factories.
– How do you make such a comprehensive request as this one?
Before the installation Hansen created a layout of the best areas to strategically place the machinery. Once the proposal is agreed, and meetings have taken place testing starts until the final completion of the project. When Brynild receives the proposal, all details are reviewed and in line with their descriptions.
Growth and acquisition
Viggo Ersøybakk is very pleased with the solution and delivery from VPK PackTech, as the installations help Brynild keep up with demand. The manufacturer has nevertheless increased sales during the pandemic, and had a record turnover in 2020.
“It shows that many people have enjoyed our products when working from home,” he says with a smile.