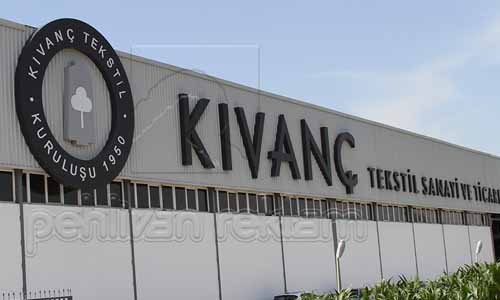
Valmet will supply an Old Corrugated Containers (OCC) line, three stock preparation lines, and an OptiConcept M container board making line with automation and services to Kıvanç Tekstil Sanayi Ve Ticaret’s mill in Adana, Turkey. Kıvanç Tekstil’s new board making line (PM 1) will produce high-quality testliner and fluting grades. The start-up of PM 1 is scheduled for the fourth quarter of 2023.
The order is included in Valmet’s orders received of the fourth quarter 2021. The value of the order will not be disclosed. A project of this size and scope is typically valued at around EUR 60–70 million.
“Kıvanç Tekstil wanted to invest in high-performance technology. Valmet offered us an interesting set of solutions and technology, including an aqua layer headbox and hard nip sizing. Since we are a newcomer in the paper industry, we were also looking for a reliable partner in this project. Valmet has a strong track record of similar successful projects,” says Ziya Kıvanç, owner representative of Kıvanç Tekstil.
“Kıvanç Tekstil and Valmet collaborated well during the sales phase; the communication between us was excellent. Almost all the meetings and contacts with the customer were via remote connections, which makes this case quite a unique experience for the whole sales team of Valmet. We as the local sales team in Turkey formed a trustworthy relationship with the customer, which was very important. Kıvanç Tekstil definitely wants to differentiate with high and advanced technology,” says Haluk Arıcan, Senior Sales Manager at Valmet.
Technical information about the delivery
Valmet’s delivery will include a new OCC line, stock preparation, and a high-speed container board machine. The OCC line is featured with a new, energy efficient drum pulping technology and fractionation. The tailored use of raw materials is ensured by including a clippings line, hardwood and softwood lines, as well as an MFC line (microfibrillated cellulose) in the full stock preparation concept. Each line is equipped with bale handling, pulping, HC cleaning, and optimized refining technology. The broke thickening and white water system fiber recovery are combined using space and energy saving filtration solution.
In addition to the OCC line, a high-speed container board machine from headbox to reeling and winding will be included. An OptiFlo Layering Gap headbox with an innovative aqua layering technology will give a very good layer coverage for the two-layer sheet that uses only one headbox and one OptiFormer Hybrid forming unit with the shoe and blade technology. This will be followed by an OptiPress Linear press section, a compact OptiRun Hybrid dyer section, and an OptiSizer Hard sizer, which provides higher strength. The end of the machine line will be equipped with an OptiReel Linear reel and a high-capacity OptiWin Drum two-drum winder. A wide scope of board machine process ventilation systems with an OptiAir high-humidity hood, starch preparation for the headbox’s aqua interlayer, continuous surface size preparation, and an OptiSizer supply system will be included as well.
Lastly, the delivery will include Valmet DNA Automation System, including machine controls, process controls, sectional drive controls, machine monitoring, Valmet IQ Quality Control System (QCS) with web monitoring and web inspection systems, Valmet Paper Lab, Valmet MAPQ freeness and fiber analyzer, and Valmet WEM wet end analyzer.
The start-up and further optimization of the new board machine will be supported remotely from the Valmet Performance Center which utilizes the latest Industrial Internet solutions available on the market. One such solution is Valmet Dynamic Centerline Advisor, a cloud-based analytic application, which generates the best available grade-based dynamic centerlines suitable for different production KPIs or properties such as energy and production efficiency or end-product quality parameters. The Virtual Mill, which can be used, e.g., for personnel training, consists of a fully digital design twin of the board machine. The delivery will also include packages of spare parts and consumables.
The board machine with a 7,250-mm-wide fabric will produce testliner and fluting grades with a basis weight range of 50–135 g/m2. The design speed of the machine will be 1,200 m/min and the daily capacity approximately 1,000 tonnes.