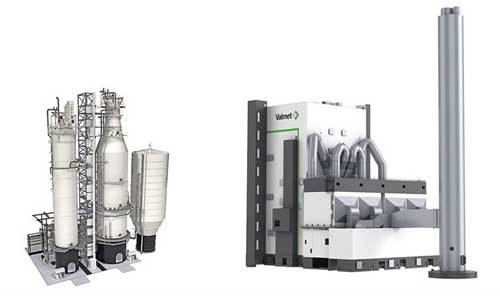
Valmet has received several pulp technology orders from Nine Dragons for their pulp, paper and board greenfield project in Beihai city, Guangxi autonomous region, in China. The order consists of two complete fiberlines, two bleached chemi thermo mechanical pulp (BCTMP) lines, a recovery boiler and DeNOx scrubbers. The deliveries will be done in phases and the start-ups are scheduled for 2023.
The value of the order will not be disclosed. However, a project of this size and scope is typically valued at around EUR 140 million. The order was included in Valmet’s orders received of the second quarter 2021.
Nine Dragons is developing its production portfolio and building pulp mills to support its new and existing paper machines with high quality raw material.
“This project is the result of good cooperation between Nine Dragons and Valmet to find the optimum mill concept solution. I am happy to say that the outcomes are state-of-the-art process solutions, which will allow Nine Dragons to produce high quality pulp grades in a more sustainable way with excellent efficiency in energy and raw material utilization. We are committed to continuing to support Nine Dragons with the latest technology and strong local presence in China,” says Zhu Xiangdong, Area President, China, Valmet.
Valmet’s delivery includes two fiberlines, two BCTMP lines, a recovery boiler and DeNOx scrubbers for recovery boiler and lime kiln with the corresponding spare part packages.
The fiberlines will provide Nine Dragons with flexibility to produce pulp grades of different types. The new fiberlines provide possibilities to optimize pulp properties with lower power and wood consumption. This allows Nine Dragons to achieve excellent resource efficiency. The deliveries include Valmet Continuous Cooking G3, Valmet Screening, Valmet Refiner and Valmet Washing, Oxygen and Bleaching technologies.
The BCTMP lines include impregnation system, high consistency refining, bleaching system, low consistency refining, screening, dewatering and washing. It is designed to provide high yield, low energy consumption and excellent pulp quality for the new paper machines.
The recovery boiler has multiple high-power features, including multi-stage preheating of feedwater and heat recovery from flue and vent gases to combustion air. The boiler is designed for low emissions and high availability. The boiler also includes non-condensable gas (NCG) incineration. In addition, the delivery includes safety related systems and Boiler Diagnostics System for the recovery boiler.
The DeNOx scrubbers for recovery boiler and lime kiln are equipped with chemical feeding in order to achieve very low NOx emissions. The process can reduce emissions under the required 50 mg/Nm3 level with high availability and low maintenance need.