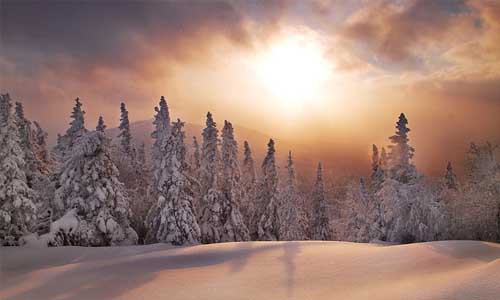
One of the largest pulp and paper manufacturers in the world has decided to invest in Heat Management’s solutions. The manufacturer has previously ordered Infrasound cleaning to their mill in Belgium and has since recognized an efficient way to conduct their steam sootblowing operations in the Nordics.
Traditional sootblowing
Most recovery boilers are delivered with traditional control systems for their sootblowers. These systems are cheap to buy but very expensive to operate, racking up millions of EUR in wasted energy. Here, Heat Management disrupts the paradigm and combines patented system controls and innovative valve control solutions, to deliver the earlier impossible solution of Sootblowing more, with less steam.
The High Impact Sootblowing System has become renowned for its way of allowing users to save a guaranteed amount of 30% sootblowing steam consumption, often even surpassing the guaranteed values.
A Swedish pulp mill.
In 2023, the order for installing HISSTM for a large mill in Sweden was received. The recovery boiler has a capacity of 2700 tDS/day, and the mill produces 550.000 tons of fluff pulp per year. Producing steam is a valuable part of the pulping process and an expensive resource to waste. The mill realized that saving significant amounts of steam was possible with HISS™, leading to higher electrical efficiency and increased power generation in the mill steam turbine, feeding more renewable power to the electrical grid.
Minimum guaranteed steam savings of 30 % means the mill will reduce their annual cost of sootblowing by saving a minimum of 8 t/h, meaning 7 GWh extra sustainable power generation and 40 GWh low-pressure steam. This is translated into reducing their mill’s annual CO2e emissions by 1950 tons CO2e/year.
A Finnish pulp mill.
Heat Management’s most recent order is a larger project and their first one for HISSTM in Finland. The main goal of this project is to save steam while sootblowing more often to stabilize flue gas differential pressures and thereby provide more ID-fan capacity compared to the current operation. The HISSTM technology will enable the customer to operate steam sootblowers twice as often as today without consuming more steam.
This mill’s result estimate is also calculated according to the absolute process guarantee from Heat Management, they are guaranteed to save a minimum of 30% sootblowing steam consumption. Which furthermore translates to 9 GWh power and 40 GWh low-pressure steam. In the Finnish pulp mill’s case, this means that they will reduce their carbon footprint by 2300 tons CO2e emissions per year.
HISS™ – Sootblow more, with less steam.
The patented High Impact Sootblowing System (HISS™) disrupts the “how we have always done it” approach to energy-intensive steam sootblowing. By operating the existing steam sootblowing system in a smarter and less wasteful way, half the steam and half the time can be saved. This leads to increased boiler efficiency, availability, and lifetime without installing any new sootblowers or rebuilding the boiler.