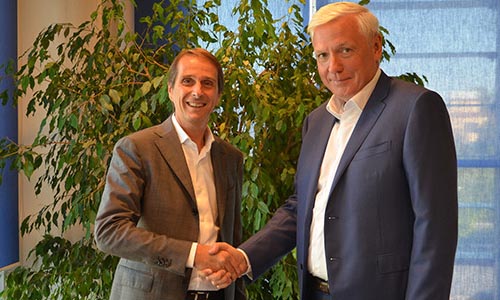
JSC “Yarpaper” selected Toscotec for a major rebuild of its paper machine at Yaroslavl mill, northeast of Moscow, Russia. PM1 has a wire sheet width of 2,830 mm, produces test liner and fluting in the range of 100 to 150 gsm, using 100% waste paper.
Toscotec will supply the approach flow system, including screens, fan pumps, TT Headbox-H fitted with dilution control system and a newly designed Fourdrinier make up. The sheet path in the press section will be optimized, including the sheet transfer to the dryer section.
Toscotec will supply a new complete dryer section, with 35 TT SteelDryers designed to operate at 10 barg, along with framing, canvas rolls, doctors, stabilization boxes, stretchers, guiding and tail threading system and the mechanical drives for the entire paper machine.
The scope also includes the engineering, erection supervision, commissioning, start-up assistance and training.
This major rebuilding project will modify the entire paper machine, including the approach flow system and sets ambitious targets of production increase and quality improvement, maintaining the same PM length, thereby reducing the impact on the existing building.
Chairman of the Board of Directors of JSC “Yarpaper”, Mr. Sergey Dotsenko, says, “This operation represents a strategic investment aimed to improve product quality, increase our production output and efficiency. As an FSC-certified manufacturer, we are focused on the sustainability of our operations. After the joint evaluation of the project, we selected Toscotec because of their understanding of our needs and development of the best technical solution in order to increase the process and drying efficiency of PM1. This is in step with boosting its capacity and expanding the product range from 90 to 160 gsm. The rebuild will be in line with our environmental standards.”
Toscotec’s Head of Sales Application Gian Luca Fornesi says, “This is our first important paper & board project in Russia. Thanks to the support of Pulp & Paper Processes, Ltd., we are glad to enter the Russian market with such a recognised producer and such an extensive rebuild, which spans from the approach flow to the wet section of the paper machine, down to the dryer section. Most sections will be newly designed, or extensively rebuilt, to achieve a substantial production increase. During the project evaluation, we assessed a number of possible solutions for the customer and we are confident that our rebuild will eliminate the main bottlenecks of this production line.”
The delivery is scheduled for August 2020.