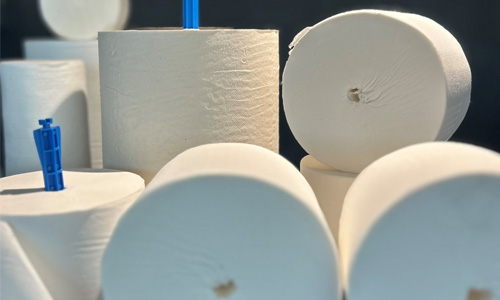
The focus of the circular economy is to extend the life cycle of products and simultaneously contribute to waste reduction. It applies the rule of the three «R’s»: reduce, reuse and recycle and undoubtedly represents a business opportunity for the tissue converting industry as well.
According to Maflex, which distinguishes itself by a distinct propensity to meet specific needs, its great added value, guiding customers toward informed choices and sustainable investments is crucial. “Our tailor-made approach enables «re-solving», «remanufacturing» and «reconditioning», adding three new «R’s» available to converters.” General Manager Luca Mazzotti explains. “Maflex stands out for its highly personalized consulting support. And it aims to ‘Solve’ several issues related to the converting process that also fall within the circular economy, such as the possibility to upgrade existing machinery by integrating more advanced automation solutions or to enable, in a simple and versatile way, the automatic production of Coreless products, considered a ‘zero waste’ in the AFH tissue product landscape.”
For Maflex, awareness comes through construction design. The benefits of the Maflex Modular Philosophy begin with the shipping and installation stages, through to production and use.
Indeed, the compact nature of the modules affects their footprint, with significant reductions in transportation costs and, consequently, environmental footprint. The independence and autonomy of the modules, each with its own integrated electrical panel and all the necessary equipment for operation, ensure fast assembly times, limited production downtime and, above all, easy grafting or upgrades to existing systems.
“The Maflex modular approach favors change management: «regenerate.» Each unit can be smoothly integrated with new technologies: the processing line remains state-of-the-art according to industry developments, while adhering to a conscious future-oriented approach.”
Seamlessly upgrading avoids complete refurbishments and maximizes equipment lifespan (key in Life Cycle Assessment – LCA), promoting a circular economy that postpones disposal of obsolete machinery. “This design system, in fact, intervenes on maintenance and consequently on durability. The simplification of interventions contributes to their resilience. Individual units can be individually maintained, addressed and upgraded, ensuring efficient business continuity.” The Maflex Modular Philosophy, enables targeted and precise interventions in order to ensure operations for as long as possible and results in high residual value. “This is a very important aspect because it ensures a sustainable investment aligned with economic commitment and circular issues.” Mazzotti continues. “Each machine maintains not only its efficiency in the longest possible time but also its value over time, postponing further large investments and machinery decommissioning.”
Needs analysis is always at the forefront, and Maflex evaluates options with its customers, the possibility of optimizing systems that are still efficient or that of «Reconditioning» if necessary. “When the systems employed are no longer in line with the customer’s ambitions and the conditions are right, we offer to take back the decommissioned machines, with the intention of reallocating them to more suitable markets.” This is a practice, which even today, represents an opportunity for the tissue industry, especially in many areas of the world where technological and production needs can vary greatly. “There are many areas where this practice still proves to be critical and is an opportunity to promote an efficient and sustainable business system and to participate in the emergence of a new converting facility.”
Supporting customers in achieving certain circular goals means «Regenerating» the technologies used by enhancing them but also supporting its production ambitions by containing its consumption.
The Maflex Energy Regenerative System (MERS) introduced by Maflex in 2010, is a pioneering system that redefines sustainable energy management practices with savings of up to 20 percent. A requirement that can not only be contained but also reused. “Regeneration units allow MERS to replenish unused energy, thereby improving the carbon footprint of the equipment. MERS, by reducing the total energy demand in the manufacturing plant, helps optimize energy efficiency in one of the most demanding industries in this respect.” Ing. Mazzotti concludes.
Maflex confirms itself as a proactive partner in supporting customers, even in the area of circularity. Offering customized solutions tailored to individual needs and ambitions is the first step in mitigating impact and applying the three-plus-three ‘R’ rule in the tissue converting industry