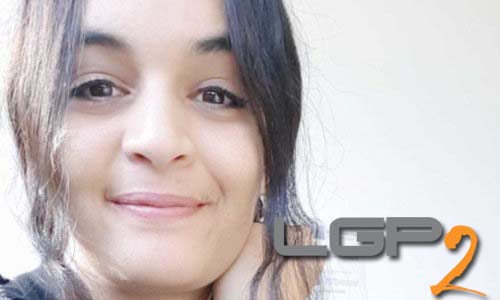
On February 9, 2022, Khaoula Bouzidi defended a doctoral thesis from the Université Grenoble Alpes prepared under the supervision of Davide Beneventi, CNRS Research Director, and of the Professor Didier Chaussy (Grenoble INP-Pagora / LGP2).
Khaoula Bouzidi presented the results of her research entitled Formulation of a thermosetting biocomposite based on poly (furfuryl alcohol) and cellulose for 3D printing.
In the last two decades, additive manufacturing has emerged as a revolutionary and influential technology. Historically, stereolithography is the first technique used in 3D printing, later followed by other processes including direct ink writing. It makes it possible to print materials such as ceramics, cement pastes and, more recently, fossil-based thermosetting resins.
In a context where sustainable development is a key subject, this thesis focuses on the creation of a new biobased printable ink using the additive manufacturing approach. This ink is composed of a blend of bio-based furanic resin, cellulosic fillers and, eventually, carbon nanotubes. The thermosetting resin provides dimensional stability, the cellulose particles enable the tuning of the rheological properties and carbon nanotubes increase electrical conductivity.
First, the rheological requirements for a printable ink compatible with the direct ink writing technique, were studied and displayed a shear-thinning behavior and a yield stress superior to 105 Pa. Later the ensuing crosslinked composites were extensively characterized highlighting high thermomechanical stability permitting to reach a material processing temperature of up to 200°C. The DIW process and the curing step were thoroughly studied and optimized in order to obtain a better printing quality and excellent interlayer cohesion.
Finally, to overcome some challenges encountered during the printing of the paste, an in situ crosslinking strategy was implemented on a 3D printer designed as part of this thesis and equipped with a thermo-regulating printing chamber between 30°C and 250°C.