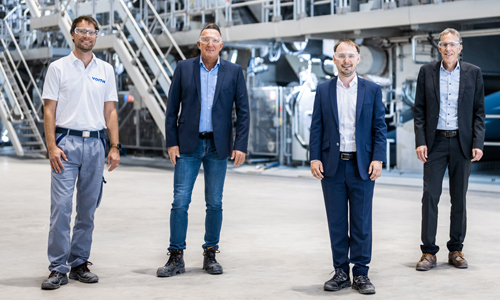
German paper manufacturer Progroup AG has successfully commissioned the PM 3, one of the most modern packaging paper machines in the world, at the company’s Sandersdorf-Brehna facility in Saxony-Anhalt. The PM 3 is set to produce 750,000 tons of testliner and corrugated medium annually. A comprehensive sustainability concept ensures the least possible consumption of resources.
Thanks to its exceptional flexibility and the close consultation between all project participants, the companies managed to complete the PM 3 within the original schedule despite the restrictions imposed by the coronavirus pandemic. “The successful startup within the planned schedule represents an important milestone in our growth strategy,” explains Maximilian Heindl, Member of the Board and Chief Development Officer at Progroup AG. “By deploying extra personnel and working additional day and night shifts, we were able to accelerate the work in such a way as to enable us to meet the commissioning date,” says René Bauer, Project Manager at Voith.
As a full-line supplier, Voith delivered the entire production line including a BlueLine stock preparation with the new IntensaDrum Duo drum pulper, which can process almost 3,000 tons of recovered paper a day. The XcelLine paper machine has a wire width of 10,000 mm and an operating speed of 1,600 m/min. The TwinDrive double unwind also included in the scope of supply increases winder capacity by up to 20 percent and allows automated full reel changes. It is complemented by the high-performance winder VariFlex Performance. The scope of supply also includes the process air and hall ventilation systems. Based on a long and successful cooperation, Voith also received a comprehensive startup clothing package for all sections of the paper machine.
Other key innovations include the closed water loop that Voith developed in collaboration with Progroup. In this system, all water used in the paper production process is cleaned in the company’s own water treatment facility using anaerobic and aerobic biological treatments and is then returned to the production process in a resource-conserving manner. This allows a wastewater-free paper production process.
Thanks to the integrated water treatment plant, we save about 3.75 million liters of fresh water annually. This is equivalent to the water consumption of more than 80,000 people.Maximilian Heindl, Member of the Board and Chief Development Officer at Progroup AG
“The Eco-Management and Audit Scheme (EMAS) certification of the European Union verifies the sustainability of our facility.” For the new facility, Progroup is additionally investing around €100 million in resource-saving technologies and environmental protection, explains Maximilian Heindl.
Apart from its particularly efficient and resource-conserving operation, the paper machine is also a cutting-edge solution thanks to the components from the new XcelLine machine and equipment design. Streamlined structures and exceptional materials ensure a professional structured impression and calm overall effect. The optimization of functional elements, such as the improved walkway design of PM 3, has simplified operation. Moreover, the headbox foundation, VariFlex Performance winder and Sirius winding system have been integrated into the new design of the entire paper machine. These changes simplify maintenance work and at the same time improve occupational safety.