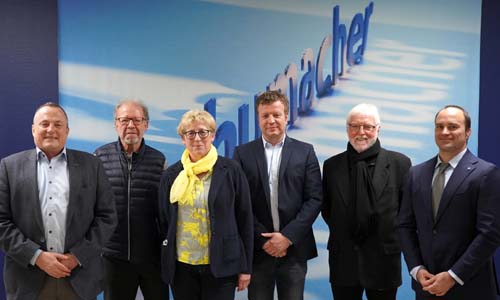
The Schumacher Packaging Group, one of the leading manufacturers of packaging made of corrugated board and solid board in Europe, is continuing to thrive and has obtained a majority interest in the long-standing Kaierde board mill in Delligsen, Lower Saxony. In doing so, this family-owned business has increased its overall capacity for solid board by 50 percent – from 50,000 tons to a total of 75,000 tons per year. This share is part of the most ambitious investment programme in the company’s 70-year history, totalling €700 million by 2025.
“The Kaierde board mill offers us an outstanding opportunity to expand our work in the solid board sector. When demand increases or resource shortages lead to production bottlenecks, this takeover will enable us to provide our customers with reliable future prospects, guaranteeing supply reliability in the future,” says Hendrik Schumacher, CEO of the Schumacher Packaging Group, explaining the company’s strategic decision.
Kaierde, a business based in Lower Saxony and steeped in tradition, has been an established presence on the market for over 30 years and produces around 25,000 tons of high-quality grey and brown board every year. The Gravenkamp family will remain involved even after Schumacher Packaging comes on board. Stephan Gravenkamp will continue to oversee and guide the site in Lower Saxony as CEO. Working together with Schumacher Packaging, the plan is to continue developing the site, which is currently home to around 60 members of staff. Plans to expand its capacity are already in motion.
“Both of these traditional companies have many years of experience and comprehensive expertise in the solid board sector. We firmly believe that the teams at our facilities in Schwarzenberg and Delligsen will benefit from this future mutual exchange and look forward to working together,” adds Schumacher. The Schumacher Packaging Group, which encompasses 18 sites in Europe following this takeover, already operates a board mill in Schwarzenberg, nestled in the Ore Mountains, within the solid board sector, as well as a solid board processing facility in Hauenstein, in the Palatine region.
Plotting a course for future growth
Despite the difficult economic situation on the global markets, the packaging specialist is currently investing €700 million in the expansion and development of plants, as well as in sustainable future technology. This share is, therefore, another important step in paving the way for future growth and is one of a variety of recent expansion plans set out by Schumacher Packaging. The company is currently expanding its corrugated board plant in Greven, North Rhine-Westphalia, to become a next-generation multi-mega plant. In this way, the packaging specialist is reacting quickly to continuously increasing demand caused by the e-commerce boom.
Sustainable corrugated board packaging, as well as packaging made of solid board or cardboard, are extremely popular and used in a variety of sectors. “Our cardboard packaging is made of 100 percent waste paper and is being used more and more often as a replacement for plastic packaging in the online trade and foodstuff industries,” says Leena Gaebler, Sales Manager for cardboard production at Schumacher Packaging. “In addition, cardboard is extremely compact and takes up minimal space during transport and storage. This all saves resources and lowers CO2 emissions – both ours and our customers’. Our interest in the Kaierde board mill and the associated additional capacity will enable us to meet increasing demand even more successfully in the future.”
Climate-neutral production by 2035
Additionally, the Delligsen site in Lower Saxony is part of the Schumacher Packaging Group’s overall strategy to achieve climate-neutral production by 2035. “We are excited to build a sustainable future for our site and our dedicated employees as part of the Schumacher Packaging Group and to enable further growth, says Stephan Gravenkamp, CEO of the Kaierde board mill. “After all, one thing is clear: Together, we can overcome the current challenges and requirements of the market, such as CO2-neutral production, even more easily and successfully.”