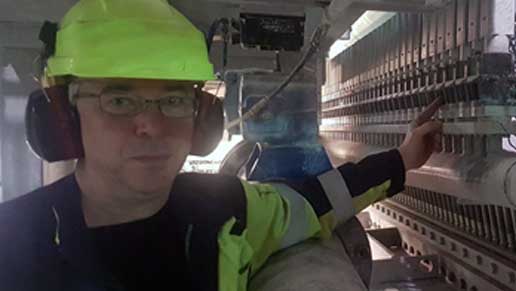
With over 30 years of experience in serving the paper industry, Tasowheel is the leading provider of dilution actuators and valves for all paper machine needs. Lately, the company completed yet another successful dilution valve change at Norske Skog Saugsbrugs.
The reliability of profiling actuators and valves is a key quality factor in the paper production process. When working properly, they ensure minimum profile variations, thus improving paper quality and increasing production efficiency.
Accordingly, dilution valves can cause major profiling errors and runnability problems if they are not operating correctly, says Tasowheel Sales Manager Jukka Ahlstedt.
The wear of the dilution valve, often caused by cavitation or fillers, may be a reason for quality problems or even web breaks. The problems may continue for a long time before their source is identified.
The material plays a critical role in valve wear. Plastic parts inside the valve increase the risk of premature wear, which may remain unnoticed underneath the faultless outer surface. This can result in sequential web breaks and other severe production problems, Ahlstedt explains.
Consequently, if the dilution valves contain plastic parts, the valve change is required every few years or sooner: in extreme cases the plastic is worn out within a year. Committed to uncompromised quality and sustainable production, Tasowheel manufactures valves that are made solely of stainless steel (AISI 316) and contain no plastic parts.
Regardless of the original manufacturer, it is possible to replace any dilution valve with our 100 % stainless steel valves, also in single units, Ahlstedt says.
Better profiles at Norske Skog Saugbrugs
Norske Skog Saugbrugs represents the latest in the series of successful valve replacements. The old steel valves at PM 5 had served the paper machine for almost 15 years, and they had gradually begun to suffer cavitation. This indicated an increasing problem in the future.
We were running at quite high dilution ratios, so we expected to get a decreased ratio and lower pressure differences in the headbox after the valve change. We also hoped that this would lead to better profiles, says QCS Specialist Trond Andreassen.
Norske Skog Saugbrugs chose Tasowheel as a partner due to their ability to deliver the turnkey solution including cutting-edge valves and their installation. In October 2018, 109 dilution valves were replaced by new RDV-90 degree valves (rotating dilution valves with 90 degree flow angle), specially designed for harsh operating environments. The new valves are 100 percent maintenance free with an excellent wear resistance and long lifetime.
The valve change was committed during a preplanned shutdown, in a tight 2-day schedule. The first improvements were immediate.
We noticed a remarkable reduction in the dilution ratios and less pressure difference in the headbox. This will definitely reduce the cavitation of the dilution valves and minimize the threat of other problems, like web breaks, Andreassen reports.
As the valve change was part of a wider QCS upgrade program at Norske Skogs Saugbrugs, more improvements in the quality and productivity will be seen after the total upgrade is complete.