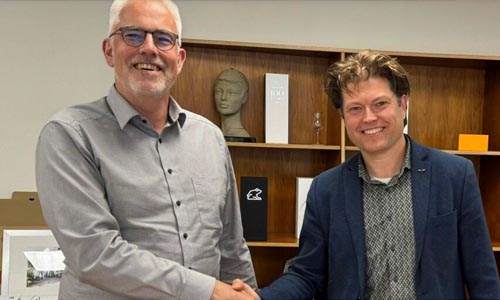
Often, the paper industry finds itself in direct competition with the makers of plastic packaging, but the Dutch recycled solid board manufacturer, ESKA, which is part of RDM Group, is creating a sustainable material that can be used for packaging.
- Companies sign agreement to develop world’s first full-scale PHA[1] biomass plant
- It will use process water from recycled paper processing to produce biomass from which PHA can be extracted
- This circular solution provides a feedstock for biobased, biodegradable biopolymers which have applications ranging from packaging to medicine
- The plant will transform waste material into a valuable resource and could provide a model for other mills
Organic material contained in the process water from the manufacturing of ESKA board at its Hoogezand plant in north-east Netherlands will be used to produce a biopolymer by fellow Dutch company Paques Biomaterials. This biopolymer, called PHA, has the double benefit of being both biobased and biodegradable.
The opportunity arises because many producers of paper – particularly for corrugated cardboard packaging – are using an increasing amount of starch to help maintain the strength of their products. This starch (much of which comes from potatoes) ends up dissolved in the process water of manufacturing mills that use recycled cardboard as a raw material. The ESKA board production plant in the Netherlands is one such mill and with its state-of-the-art closed-loop water system the increased starch content has been affecting operations.
Finding a more circular solution
RDM Group, under the leadership of the Dutch team, has worked in cooperation with Paques Biomaterials over the past 10 years to resolve the challenges and has developed a more circular solution. In a new plant, the process water will be fermented and aerated in a series of biological reactors to form a specific type of biomass that will then be dried into a powder. The treated water will be returned to the mill. The drying process will use heat energy captured from the bioactivity itself – and any excess energy can be fed back to the mill.
Paques Biomaterials will then take this biomass powder away and turn it into an estimated 2,000 tons a year – or 70 truckfuls – of PHA, or polyhydroxyalkanoate. PHA is similar in look, feel and performance to plastics produced from fossil fuels. Because it comes from a renewable, biobased resource and is both biodegradable and compostable, PHA offers the possibility of a sustainable alternative to traditional, non-biodegradable plastics.
As well as being suitable for food and beverage packaging, PHA has the potential for use as a biodegradable barrier coating or adhesive in RDM Group’s own recycled cartonboard products, increasing the circularity of the Company’s operations.
Next steps
Having successfully completed a pilot project to produce PHA, a dedicated joint venture will be created to complete the industrial business case feasibility study and apply for the necessary permits. If the concept proves to be successful and the permits are granted, then the plant will be operational by 2027.
“As a B Corporation,[2] we look at everything we do to find circular solutions that are really good for society,” says Bert Bodewes, ESKA’s Manager, Corporate Social Responsibility. “By building the world’s first industrial water purification system, which both purifies process water and produces PHA, our process water, which was previously worthless, becomes a valuable organic waste stream. If the PHA produced can then be used in our own products as a biodegradable barrier coating and/or adhesive then that will be circularity at its best.”
“The construction of the first full-scale PHA biomass plant is a global first in the PHA industry, but also in the paper industry,” says René Rozendal, co-founder of Paques Biomaterials. “By producing PHA in the process water, you can create value with water purification. Moreover, it is particularly interesting for companies that, like ESKA, want to work on zero liquid discharge solutions.”