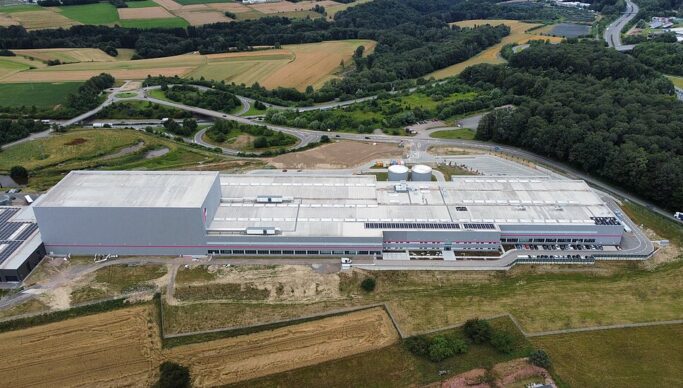
The latest Progroup corrugated sheetfeeder plant in Petersberg near Frankfurt has been in routine production since the beginning of August. The Landau-based family company is extending its leading market position with its ultra-modern production site close to Pirmasens which will also create a combined total of 60 new jobs and training positions.
Progroup can celebrate reaching yet one more mile-stone. Since the beginning of August the first corrugated board sheets have been routinely coming off the end of the line in the latest plant (PW15) in Petersberg. “We are systematically pursuing our growth strategy and are strengthening our market position even further with this investment. As a family company rooted in the region, the plant is also a clear commitment to the Palatinate as a place for work and business,” stated Maximilian Heindl, Chairman of Progroup’s Management Board.
Progroup began operating its first plant in Offenbach an der Queich more than 30 years ago. In addition, the Group Office, or administrative headquarters, of this paper and corrugated board manufacturer is located in Landau.
Impressive figures
PW15 is yet further proof of Progroup’s technological leadership. Ultra-modern processes and innovative manufacturing technology form a perfect partnership here that guarantees corrugated board of the highest quality made by extremely efficient manufacturing methods. The site has the very latest high-tech plant and equipment capable of manufacturing up to 200,000 tonnes of corrugated sheetboard per year. The production line runs at a speed of 400 metres per minute. The speed at which the project was completed was also impressive. The ground-breaking ceremony took place as recently as June 2022. The rapid completion of the project is due primarily to Project Manager Rudolf Vervoorst and his team.
Exceptional energy efficiency
A clever concept provides a sustainable source of energy. Two super-efficient combined heat and power plants plus a photo-voltaic plant on the roof cover the works’ total energy requirement for two-shift operation manufacturing corrugated board. This also reduces the consumption of fossil fuels. The modern combined cooling, heat and power plant uses the waste heat from its own power generation either to generate cold, or alternatively to feed heat into the heating circuit, as required. “This system is so efficient that we not only save energy in the manufacturing processes but can also heat the 30,000m2 building in winter and cool it in summer” explained Maximilian Heindl.
Successful packaging park model
In Petersberg Progroup has repeated its successful packaging park model based on a long-term partnership. PW15 was erected directly adjacent to the production facilities of Progroup’s long-standing customer G&G Preisser, resulting in major advantages for both parties: Progroup corrugated board stacks from the fully automated high bay warehouse with 15,000 storage spaces are now transported by a conveyor belt directly into Preisser’s packaging plant. The smart intralogistics system always knows exactly when and where each stack has to go, and replaces deliveries previously made by road. This not only eliminates significant costs for the two partner companies but also benefits the environment by removing the need for several dozen truck movements each day.