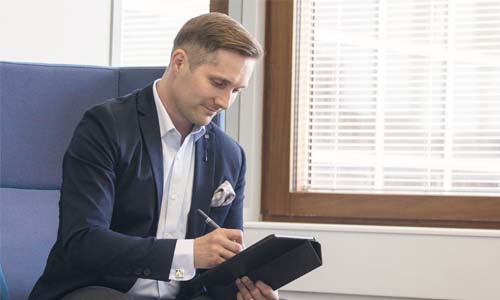
Implementing digital services for paper and board mills
Imagine if you had a crystal ball that would let you see hours into the future. What would you want to know? If you work at a paper or board mill, chances are you might want to anticipate runnability and quality issues. That way you could course correct before headaches even happen!
Well, you don’t need a crystal ball ─ there’s something better. Thanks to machine learning and predictive analytics, today paper and board mills can process massive amounts of data every minute and make thousands of calculations almost instantly. These new digital solutions offer accurate, data-based predictions designed to help you improve quality, act faster and optimize costs.
When I think back to the way the industry used to analyze data manually, I’m truly amazed at the progress we’ve made with new technology. At Kemira, we began piloting our
predictive analytics in 2018. Increasingly, we see mills embracing digital solutions that optimize all aspects of operations right down to the chemistry ─ which, by the way, is an important area that has implications for the entire paper and board making process.
Getting started
While many paper and board mills are familiar with real-time monitoring and automated dosing technologies, most are just starting to learn about and implement predictive analytics. If that sounds like you, then you probably have a lot of questions and that’s normal.
I like to start by explaining the key benefits, so customers understand the value straight away. With predictive analytics, paper and board mills can:
- Gain insight by pinpointing the root causes of process instabilities
- Stabilize the production process with continuously balanced wet end chemistry
- Make faster, fact-based decisions in mill operations
It also helps to understand the ecosystem. Generally, the players include the paper and board mills (who provide the data), technology providers and automation solution providers.
Common challenges: data gaps
Customers often have concerns about the challenges related to adopting these new technologies. One that’s nearly universal is data privacy. I want to stress that data remains the property of the paper and board mills. At least, that’s how Kemira does business. Still, mills can be reluctant to share vast amounts of data because of security concerns and confidential business information. Unfortunately, that can have an impact. Data quantity is linked to data quality. Quality data equals quality predictions, which ultimately means
customers get more value.
Another challenge is ensuring that cloud-to-cloud connections are working well. That connection must be stable to ensure no live data is missing. You don’t want data gaps because, again, that affects the quality of predictions.
And, finally, there is one other area that usually flies under the radar: chemistry.
Chemistry offers key data points
Papermaking is very dynamic and complex with lots of constantly changing variables. One of the most complicated is chemistry. All mills understand the importance of chemistry. But that’s different than understanding the chemistry itself.
Digital solutions finally provide a way to automatically gather intel about these little-understood phenomena that impact runnability, end-product quality, and the overall efficiency of machinery. But that only works if the chemistry is measured correctly and prioritized by the algorithms in whichever solution you choose.
Kemira’s digital offering, Predictive Wet End, nicely builds on our decades-long history of chemical expertise. Unlike some other solutions offered by the major machine learning companies, which tend to focus on the mechanical aspects of the papermaking process, we focus on providing an understanding of what’s happening on the molecular level. To us, this makes sense since chemistry impacts mechanical performance.
Of course, digital solutions don’t have to be either or. Kemira Predictive Wet End can be used as stand-alone solution or combined with other digital offerings. In my opinion, the paper and board mills that apply AI and predictive modelling that draw on both mechanical and chemical data points will ultimately be the winners in this new digital era.
Economic and environmental pay off
Those who harness the full power of digital technologies can get huge economic and environmental payoffs. They can cut down on the number of rejected reels and reduce production downtime. Digital solutions also deliver savings by reducing pulp, water and chemicals consumption.
Some board makers will realize that optimizing wet end performance lets them switch to cheaper raw materials while maintaining the same strength level.
Additionally, digitalization allows certain processes to be remotely controlled, which can reduce risk and improve occupational safety.
Digital revolution and evolution
According to the World Economic Forum, only 13% of leaders say their organizations are ready for the digital age. But from what I see, the paper industry will not be left behind.
As the digital ecosystem continues to evolve, I’m excited to be working closely with paper and board mills who are revolutionizing the industry. Kemira is helping them get out front now, and we will continue to iterate and expand our digital solutions to ensure our customers keep their competitive edge. We don’t need a crystal ball to see the future. The digital transformation is visible all around us.