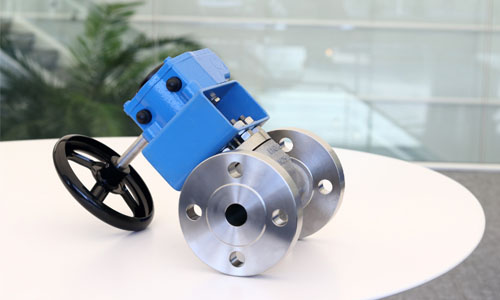
Neles has delivered its first valve with a 3D printed valve body for field testing. Except for the body, the valve is a standard T5-series ball valve made of stainless steel. It will be tested at Teollisuuden Voima’s power plant in Finland. The project is done in cooperation with Teollisuuden Voima and Fortum.
Paving the way for 3D printing in the industry
Neles is at the forefront of using 3D printing in valve applications. The company started testing the suitability of 3D printing technologies for metal components years ago and supplied the first valves with non pressure retaining, 3D printed metal components in 2018.
“The valve body is a pressure-retaining component and thus its material properties need to be well known. However, industry standards for 3D printed materials are under development. It has been necessary to test the valve body material extensively, and, for example, the tensile strength and impact resistance to make sure it is safe and reliable in the process,” says Jukka Borgman, Director of Technology Development at Neles.
The field tests will provide a lot of valuable information on the feasibility of using 3D printing to produce pressure-retaining parts with significantly quicker delivery times. 3D printing also enables more efficient use of materials and optimized flow paths in noise attenuation trims, delivering superior performance compared to conventionally produced trims.
“3D printing can help us to optimize valves for customer-specific needs in various applications and with all valve types. These tests will also provide valuable information for our product development teams, as they are constantly looking for new ways to improve reliability, performance, and material efficiency,” Borgman adds.