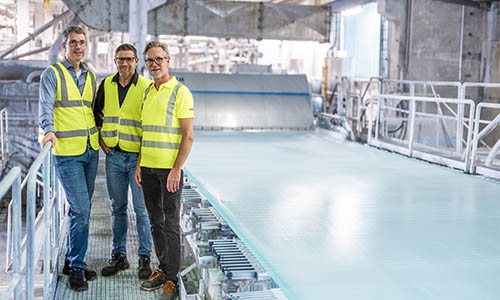
Voith‘s fourth-generation MasterJet headbox technology, the MasterJet 4Tec, is now available and has already impressed the first customers with its positive effects on operating efficiency and paper quality. The innovations result in improved jet quality and thus flawless, streak-free sheet formation, as well as a reduction in energy consumption.
The measures to further improve cleanliness and the resulting increase in machine efficiency have also proven to be very convincing.
Improved formation ensures outstanding paper quality
The headbox makes a decisive contribution to sheet formation, one of the most important quality parameters for most papers.
“Our MasterJet 4Tec sets new standards in jet homogeneity,” reports Markus Haeussler, Product Manager Headbox at Voith Paper.
The improved fiber distribution and more than 30 percent streak reduction in the jet ensure the best formation values and a perfect visual appearance of the paper.
Annual energy savings in the six figures
Significantly improved energy efficiency further ensures considerable savings in operating costs.
“The fan pump contributes significantly to the electrical energy consumption of a paper machine, and this depends a lot on the headbox,” says Haeussler. “This is why we have put a high priority on reducing the energy consumption of the MasterJet 4Tec.” On a sixmeter-wide paper machine that produces at 1,000 m/min and 80,000 l/min, and with a kWh price of €0.12, these measures can lead to annual savings of around €103,000.
Brigl & Bergmeister, a leading manufacturer of label papers, is convinced of the performance of the headbox:
“The team from B&B and Voith did an excellent job throughout the entire project,” says Josef Goessnitzer, Production Manager at Brigl & Bergmeister in Niklasdorf. “The result was an impressive start-up of the new MasterJet 4Tec. It took less than two and a half hours from stock on wire to achieving saleable paper quality. Right from the start, we had very good cross profiles, and the exceptionally smooth jet was impressive.”
With the EdgeMaster, the MasterJet 4Tec has an edge control on the fourdrinier wire that is easy and intuitive to adjust and can simply be swiveled upwards for a wire change. An innovative Teflon seal ensures a fiber-free wire edge and clean surfaces around the headbox.
“The headbox and surrounding area are very clean thanks to the new EdgeMaster from Voith, which further reduces our number of sheet breaks. Immediately, we had 50 hours without a sheet break,” says Goessnitzer. “We are really impressed with the new MasterJet 4Tec and are glad we chose this headbox.”
Khanna Paper Mills, a leading Indian papermaker and longstanding partner of Voith, is already profiting from the advantages of the new MasterJet 4Tec, too.
“From the beginning, the performance of the MasterJet 4Tec on our PM 4 has been impressive. The headbox delivers superior results after fast stabilization on the PM 4,” reports Rahul Khanna, Managing Director & Promoter at Khanna Paper Mills, which has already announced a second order. “This cutting-edge technology from Voith and the positive experience by the whole team have encouraged us to place a repeat order with Voith for another MasterJet 4Tec for our PM 5, one of the widest and fastest paper machines in India to date,” says Khanna.
The MasterJet 4Tec is the successor to Voith’s proven MasterJet Pro technology. The headboxes deliver the highest quality, outstanding efficiency and optimal operation.