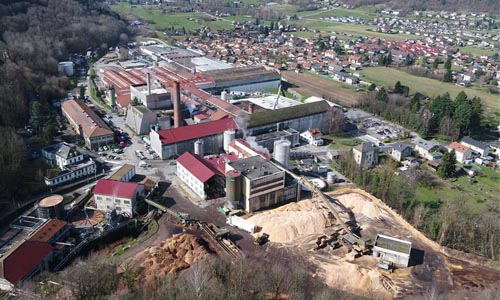
After 2024, marked by significant pressure on the packaging board market and rising costs, the French papermaker La Rochette Cartonboard announces “a significant strategic renewal” with a plan entitled “Towards New Heights,” focused on responsiveness, reliability, and transparency. The objective of this “Savoyard” (in the Alps) producer of virgin fiber-based cardboard for the food, pharmaceutical, and premium sectors: to return to a sustained growth rate this year, to quickly reach revenues exceeding €115 million and increase productivity by 10% per year by 2027. In terms of production, a volume of 120,000 t is planned by the end of 2027, compared to 88,000 t in 2023 and 90,000 t in 2024.
To achieve this, the company will activate three levers.
On the one hand, it will innovate and develop new growth drivers with a stronger presence in its traditional markets, while expanding into new markets and customers, particularly in the United Kingdom and Europe. To achieve this, it will rely on strengthening its product innovation and developing tailor-made solutions. A new range of kraft cartonboard, for example, will enrich its offering this year.
“This customer-centric approach is at the heart of the company’s repositioning,” says Béatrice Jacquet, CEO of La Rochette Cartonboard, who succeeded Christophe Lloret Linares (who left the company and the Mutares group at the end of 2024). “We want to create shared value, build trust, and evolve industry standards.”
On the other hand, investment and transformation. A program is already underway, which includes a €10 million investment in the biomass boiler in 2023 and €1.5 million in 2024, dedicated to the refining modernization. By 2027, new priorities have been set for production lines, logistics, quality control and the work environment. The company will thus accelerate its transformation around six key areas (work environment, performance, simplification, development, agility, transversality).
In parallel, an internal transformation program will be based on around 50 continuous improvement initiatives led by employees, such as the 5S method (optimization of workspaces), Lean (waste reduction) and Waste Management.
Finally, the third area of focus is to mobilize resources and partners. Some fifty interdepartmental working groups will be activated by the end of the year, and more than fifteen new hires are planned in manufacturing, support, and sales functions. In addition, 30% of employees will receive training each year in continuous improvement methods and quality of life at work.
The company, which has 280 employees, also aims to create collaborative working groups with its customers, suppliers, and other key local stakeholders. The objective is to identify performance levers in quality, procurement, logistics, and traceability. This plan also provides for strengthening efforts in the area of ecological transition, with concrete commitments by 2027 (20% reduction in waste, continuous improvement in energy efficiency, certifications and continued partnerships with sawmills and communities).
Valérie Lechiffre