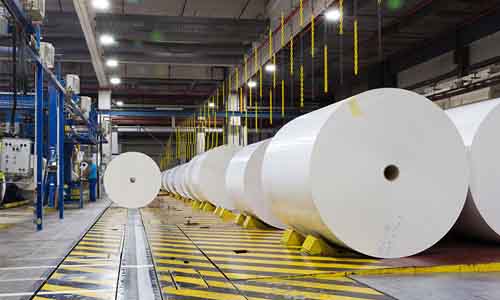
At the beginning of 2022, the entire shipping logistics of Konvertia Germany GmbH (formerly known as Pyroll Germany GmbH) were converted in a record time of two months.
The challenge was that, for operational reasons, the dispatch logistics had to be transferred back to the company from an external service provider at short notice, with the project to be completed within three months. In addition to this, equipment, staff and IT systems also had to be procured as part of the project. Conducting the project during the festive period and new year, as well as a rebranding of the company, made the situation more challenging.
Konvertia Germany GmbH were not able to complete this project with their internal resources, as they do not have an independent IT department to fulfil the requirements of the project. WM-data Germany, which had already delivered the BDE solution used at Konvertia, was commissioned with the implementation as a nearshore specialist for the paper industry.
The business model of Konvertia, which consists of assembling rolled goods for customers on behalf of its business partners, requires the handling of finished goods in the form of rolls and sheet pallets, as well as a large number of warehouse additions from different partners, especially in the logistics area. Since time-critical data was being exchanged between Konvertia and their partners, this important information could not be neglected.
Due to the short time available, a scrum project based on the FAGUS Paper Solution was chosen. With the company’s stance on the pandemic and the time sensitivities in place, small virtual workshops were implemented. Process analysis was carried out with the team at Konvertia, the detailed concept was created step by step, while the necessary hardware resources were ordered and tested remotely.
Konvertia ‘s existing warehouse had previously been managed by an external service provider, including the company’s IT. Since the new infrastructure such as forklifts, scanners and staff were not yet available, the tests had to be heavily improvised. Procedures were created and checked using test data, while Konertia’s real-time stock inventory was to be imported into WM-data’s FAGUS solution by the agreed start date.
With the teams at Konvertia and WM-data working together closely, and a clear prioritisation of the tasks and necessary preliminary work, the project would not only meet the proposed changeover date but exceeded expectations.
Oliver Spraul, Managing Director of Konvertia Germany GmbH, spoke of his satisfaction with the changeover: “We couldn’t have done it alone, there were too many tasks to be done at the same time. It was the right decision to entrust WM-data with the entire task. A big thank you goes to the teams at WM-data and Konvertia for their great commitment. We are pleased that we were able to implement our ambitious goals for optimising the flow of goods at such short notice. I assume that we will be able to support our customers more flexibly in the future.”
Managing Director of WM-data Germany, Alexander Boden, is also delighted with the timely implementation: “We are currently still working on further additions and the processes to optimise. Such a project, especially if it is carried out remotely, can be managed well if there is a good, trusting relationship with the customer and we are particularly pleased about that in this case.”