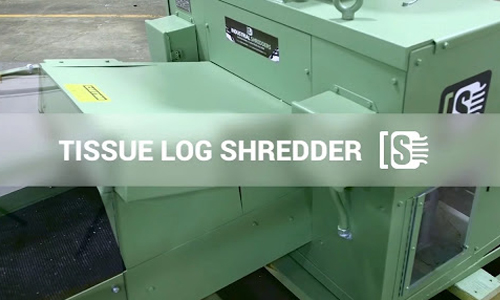
Industrial Shredders, which builds complete systems that solve waste challenges from start to finish, has been safely and diligently supporting its customers as they manufacture the essential tissue products that are in such high demand these days.
Companies such as Procter & Gamble, Georgia Pacific, Clearwater Paper and First Quality all rely on Industrial Shredders for tissue log shredders, which remove reject tissue logs from the converting line without requiring a person to pick them up. This automated process enables social distancing by reducing the number of people on the process line and makes the re-pulping process more efficient.
“Our shredder is attached right to the converting equipment, so the scrap logs are discharged directly into the shredder and then air handled to the re-pulper or baler,” said Industrial Shredders CEO David Barnard. “Right now, companies are trying to knock out as much tissue [and towel] as they possibly can. If they have someone running around picking up reject logs off the floor and then physically wheeling them away, that’s not really efficient or entirely safe.”
With increased tissue production comes well-used cutter heads, and Industrial Shredders has been up to the task as refurbishment jobs pour in from customers.
“Over the past eight weeks or so, we’ve refurbished as many cutter heads as we did all last year,” reported Barnard. “When they come in, we inspect them, sharpen them and ship them back within a week to help keep the lines operating smoothly. We appreciate their attention to maintenance and want to support them.”
While staying busy supporting its customers, Industrial Shredders is complying with current government, C.D.C. and W.H.O. ordered/recommended health procedures. Safety precautions being enforced include employees washing hands frequently throughout the day; taking every employee’s temperature upon entering the building; reporting any suspected COVID-19 cases and exposure to the local health district; keeping employees apart with separate work areas and barriers; requiring everyone in the building to wear protective face coverings; disinfecting all communal, high-contact surfaces before the end of each shift; disinfecting any shared or communal tools after each use; and limiting shop hours to Monday through Thursday.
“We’re just remaining true to our identity; we’re a small, American-owned business with a ‘roll up your sleeves and get to it’ personality,” added Barnard. “Keeping our employees safe and healthy is a high priority, as is supporting our customers who deserve to receive great appreciation for providing tissue essentials during these challenging times. We’re proud to be the little guy behind the scenes with a lot of hard-working people who do the job right.”
RELATED NEWS
Italia Technology Alliance (A.Celli Group) acquires Sipack
March 31, 2025
Sonoco named one of America’s most trustworthy companies
March 28, 2025
Golbey to start containerboard production in April
March 27, 2025
TAPPI Journal awards Best Research Paper for 2024
March 26, 2025
New Valmet office opens in Tikkurila, Vantaa
March 20, 2025