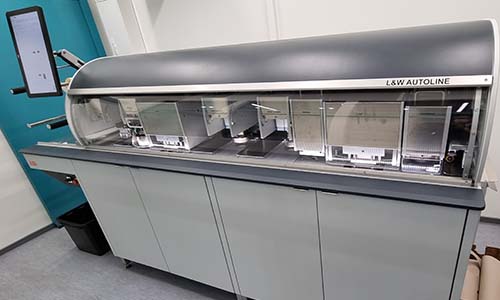
Containerboard manufacturer Papierfabrik Adolf Jass Schwarza GmbH has successfully integrated ABB’s latest L&W Autoline automatic testing solution into its production process, largely replacing manual laboratory measurements.
The move is part of wider digitalization project at the mill, which produces one million tons of corrugated base papers annually, and brings quality inspection closer to the production floor. Jass operators will gain reliable quality insights faster, enabling them to adjust the process and parameters to ensure increased efficiencies through fewer rejects, saving energy and raw materials usage.
Quality data from the L&W Autoline is collected in the mill’s quality management system via integration with the ABB Ability™ System 800xA distributed control system and OPC communication, thus adding automated laboratory data to the mill’s universal view of product quality.
“The integration of L&W Autoline automatic paper testing means we have completed the move from time-consuming manual paper testing so that our personnel can focus on quality adjustments and optimization for our end products,” said Dr. Uwe Weiss, Technical and Production Manager, Jass. “We are highly satisfied with its performance and already see the benefits of having more quality data in less time.”
“Reducing measurement uncertainty or test variability is at the heart of what automating paper testing systems can provide paper mills, enabling papermakers to make more informed decisions and take quicker corrective action,” said Felix Schäufler, Sales Specialist, ABB. “The addition of the new L&W Autoline, with the latest software standards, provides closer production control, therefore reducing the number of rejects and saving Jass both energy and raw materials.”
ABB’s next-generation L&W Autoline is the fastest and most reliable automated paper testing solution. It meets current industry standards (ISO/TAPPI) and delivers accurate and repeatable quality reports in minutes, allowing production to react faster to process disturbances.