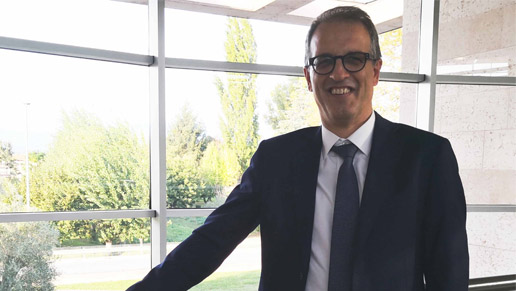
Six months after its disclosure, Fabio Perini Spa takes stock of Digital Tissue™, the suite of digital solutions for the tissue ecosystem aimed at optimizing the overall equipment effectiveness (OEE) of the lines: as of today, over one hundred thirty lines all over the world (between Europe, the Americas, Asia and Africa) are connected to the Lucca headquarters allowing to constantly control the fact-based production thanks to a “graphic thermometer” which keeps the customer and Fabio Perini engineers up-to-date on the machines’ status in an intuitive way.
“The aim of Fabio Perini – Antonio Mosca, Head of Fabio Perini S.p.A Digital Transformation, comments – is not only to be a supplier of converting and packaging lines, but also to offer a complete digital proposal, with smart software and controllers which, by collecting the data directly from the machines, can allow management of the whole production line, optimization of the output and definition of specific KPIs”.
“With Tissue Data Cloud – Mosca adds – we have concretely demonstrated the potential of the new digital services to our customers. Data collection and analysis, processed into easy and intuitive indicators, offer immediate evidence of the machines’ performance, while the detection of irregular trends allows our technicians to put in place immediate actions to recover the efficiency of the production line. However, our objective is to go beyond emergency rescue, that is to be able to predict potential anomalies and propose a “treatment plan” personalized for each customer”.
The future of Digital Tissue™ is not limited to single machines or lines. “We want to see the machine integrated with the line and we are preparing to receive data both upstream and downstream from the machine, so as to realize an integrated OEE for the line, all the way to being able to analyze the performance of the whole plant. Our dream – and an operational plan already exists to realize it – is to integrate the plant with the overall production chain, from the tree in the forest to the tissue roll in the household”.
Digital Tissue™ revolves around four pillars:
Tissue Data Cloud
Data processing through several performance indicators offers the customer immediate visibility of the critical steps of the process. By using a dashboard, directly accessible from the Fabio Perini Customer Service Portal using PC, Tablet and Smartphone, the data of the lines are processed in an easy and intuitive way. Thanks to the analysis of these indicators and to the expertise of the company technicians, customers are offered a real Digital Audit enabling them, even remotely, to detect the causes of line malfunctions and to establish ahead of time the actions to solve them.
Process Control
Process control is a service and solutions package which now can be installed not only on all the new converting lines, but also on installed bases already operating in production. Thanks to Process Control, the tissue ply and the finished product can be measured and the data collected to be converted into information that is useful for productive efficiency.
All-in-one
All-in-One is the Smart Application that allows automatic management of the change of format of the whole line by communicating the type of recipe and the configuration of production parameters. In addition, All-in-One manages the line’s output flow and can modify the speed of each machine by modulating the capacity of the accumulator, allowing the operators to act without interrupting production.
Condition Monitoring
Condition Monitoring is a solution for predictive maintenance that, thanks to vibrational analyses, pinpoints possible anomalies or deviations from planned patterns, allowing to plan maintenance on the basis of the actual status of the equipment and avoiding untimely stops or unnecessary replacements.
Digital Customer Service,
The WECARE platform together with the processing and analysis of production data, combined with the technical expertise of the Fabio Perini staff, enables customers to preserve the value of their capital asset over time and to optimize the Overall Equipment Effectiveness (OEE) of their lines.