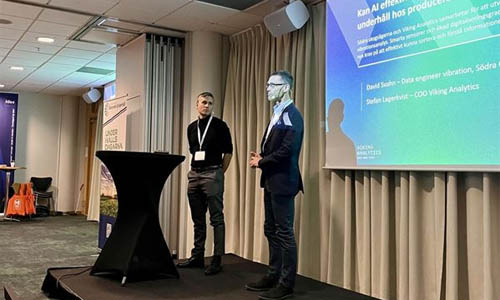
The Maintenance Days, organized by the National Organization for Swedish Maintenance, gathered professionals from diverse sectors, including the engineering, process, mining, and steel industries. The event featured a carefully curated lineup of speakers representing academia, industry, and security firms, focusing on the latest innovations and strategies in maintenance.
Maria Stockefors, CEO of Swedish Maintenance, opened the event with a call to action:
“The Maintenance Days are focused on networking. You who have come here have enormous competence, and we have a lot to convey to each other. Together we build a strong industry.”
She emphasized the vital role of maintenance in driving profitability through reliability:
“It is important to bring out and talk about and understand the importance of maintenance. With reliability comes increased profitability. We have to see which interventions have the greatest effect, be innovative, and constantly develop skills.”
Among the presentations, one notable case study showcased by David Svahn, a vibration data engineer from Södra Cell, and Stefan Lagerqvist, COO and co-founder of Viking Analytics, highlighted the transformative power of AI and smart monitoring technologies in optimizing maintenance strategies.
Transition to Wireless Sensors
Södra Cell is moving away from traditional hand-held vibration measurement instruments in favor of wireless sensors. Currently, 3,000 sensors are installed, with a goal to complete the transition by 2027–2028. These sensors offer continuous monitoring, eliminating the need for manual rounds.
Despite the advances, the system generates approximately 1,100 alarms weekly, handled by only two engineers. Alarm thresholds are often determined based on intuition and require frequent updates. While existing tools like data filtering offer some relief, the need for more robust solutions is evident.
Role of Viking Analytics and AI Tools
Viking Analytics has developed Multiviz, an AI-powered tool aimed at revolutionizing vibration analysis. Currently tested on 5% of Södra Cell’s sensors, the tool analyzes data across thousands of machines without requiring:
- Machine-specific details
- Pre-set manual alarm thresholds
- Machine type classifications
Initial results reveal a significant reduction in workload, saving engineers 2–3 hours of analysis daily with just 5% coverage. Full-scale implementation could result in even greater time and cost efficiencies.
Case Study: Predictive Maintenance in Action
David Svahn illustrated the potential of predictive maintenance through a real-world example involving a screw conveyor in a washing press. When vibration data flagged a warning, a manual inspection revealed a damaged belt. The issue was resolved during a scheduled maintenance stop, avoiding an emergency shutdown.
The effectiveness of the repair was subsequently validated using both Multiviz and Södra Cell’s traditional tool, CondMaster, showcasing the complementary strengths of advanced and conventional systems.
Benefits and Future Prospects
Smart sensors and AI tools like Multiviz allow early identification of issues, minimize manual labor, and significantly improve efficiency. While only 5% of sensors are currently integrated, the potential impact of expanding this to 100% highlights the value of digitalization and AI in industrial maintenance.
These innovations align with Södra Cell’s commitment to sustainability, operational excellence, and industry-leading practices.