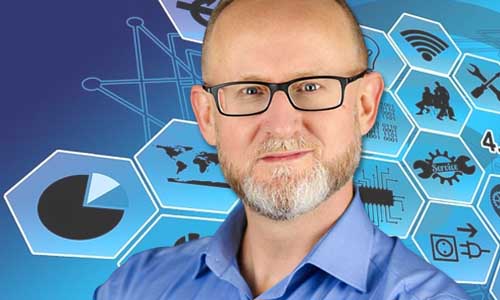
Rising costs, difficulties in supplying raw materials, new environmental demands from consumers… The paper and packaging industry has not been spared by the Covid-19 crisis and changing consumer habits. In order to remain competitive in this very dynamic market, paper and packaging manufacturers have had to find ways to improve their results. To make a significant difference, more and more manufacturers are finding more intelligent ways to use the data they create. Factories produce massive amounts of data, which represents an incredible source of wealth for those who are able to gather and use it for business optimizations.
Braincube has more than 250 customers (CAC40, SME & Midcaps) in 35 countries around the world. With headquarters in France, Brazil and the United States, they provide solutions that meet today’s growing reliance on production data. Braincube has developed a specific expertise within the paper and packaging industry. Over the last decade, they have collaborated with many of the leading paper companies includingOji Paper, Sappi and Smurfit Kappa.
These companies leverage Braincube for automated SPC reporting and product-based Digital Twins for centerlining and process optimization. For Smurfit Kappa, Braincube was first used to identify the best operating parameters for a newly implemented machine. After
seeing success with this use case, they chose to scale this solution to other factories. Their goal is to continue optimizing their already efficient factories by relying on Braincube’s AI to make additional discoveries.
Oji Paper worked with Braincube’s ready-to-use applications to identify the ideal use of raw materials. This led to a 10% savings from chemical inputs and 5% less chemical inks used in their specialty papers in just a few days.
With its SmartIIoT platform and its knowledge of manufacturing processes, Braincube helps paper and packaging manufacturers meet their greatest challenges and thus improve their performance:
⮚ Reducing unplanned downtime: unplanned downtime strongly affects productivity. In order to limit these production incidents, Braincube assists in modeling the manufacturing process using digital twins and industrial data. This allows a better and more precise understanding of the conditions related to breakages and stoppages.
Benefits:
● Optimizing production through an optimal configuration of the process.
● Reducing operating hazards with real-time recommendations, that continuously adapt to changing conditions
By eliminating downtime through real-time recommendations, Braincube supports operational teams in their strategy to improve asset performance.
⮚ Improving quality: Continuous improvement is fundamental to increasing the quality level of production, reducing waste and ensuring stable production costs over time.
Intelligent analysis of production data, combined with the CrossRank algorithm, allows the desired quality level to be selected and maintained over time.
Benefits:
● Providing technical teams with a comprehensive analysis of historical data and ranking the variables that have the most impact on industry
objectives.
● Receiving recommendations for optimal settings on equipment to achieve a specific result. Technical teams can verify these recommendations, define rules, alerts and parameters, and then send changes directly to the shop floor for implementation. This ensures that the best possible production can be reproduced under any circumstances.
IIoT thus allows paper and packaging companies to digitally see the impact of formula changes (before they are put into production) and evaluate the outcome. They can choose whether or not to implement the AI recommendations and come up with a closed-loop production.
⮚ Improving Overall Equipment Effectiveness (OEE): to better control yield fluctuations, Braincube’s IIoT platform centralizes cleaned and structured data from Braincube’s Digital Twins in an intuitive interface for users. They can then create customized and interactive dashboards in the Studio application, to get an accurate view of real-time and/or historical production data fromEdge and/or Cloud.
Benefits:
● Allowing all the members of the operational teams to have a better visibility on the indicators which compose your global OEE (availability, performance and quality). Braincube’s OEE application automates calculations and facilitates real-time monitoring.
● Using continuous, real-time data, as opposed to a post-production SRT calculation, it is possible to solve a problem without wasting more time, product or equipment.
● Identifying the underlying causes of lost productivity. To facilitate immediate adaptation of strategy on the factory floor, the application also displays the most likely reasons why a company is experiencing production limitations.
The OEE application saves time and effort, and gradually improves its indicators as new data becomes available.
⮚ Minimizing costs: With the Advanced Analysis application, teams can meet precise product specifications while producing products at a lower cost. For example, by identifying suppliers which provide better product quality, replacing fibers with chemical substitutes, or determining the impact of different moisture levels on scrap.
“The paper and packaging industry has always been competitive, but the stakes are now higher than ever. IIoT allows these manufacturers to achieve tangible goals, while giving employees the tools to make continuous improvements,” says Laurent Laporte, Co-founder & CEO of
Braincube.