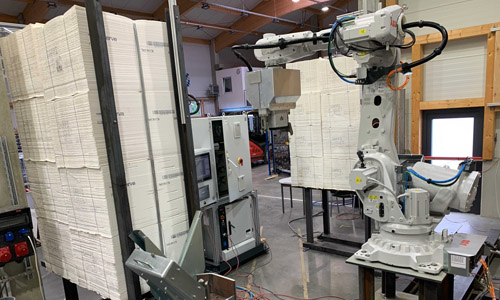
The specialist for automation solutions cts GmbH offers a new, highly efficient robotic solution for the dewiring of pulp bale units in the incoming material area of companies from the “Pulp and Paper” sector. Up to 28 of the bale units weighing tons can be dewired per hour fully automatically with the cts dewiring robot DWR-U. By this, 1 robot can serve 2 or more independent lines in parallel! The flexible robot with electromechanical drives not only saves energy and space, but also protects the pulp from contamination by hydraulic oil. Another benefit: robot-assisted de-wiring significantly increases safety for the employees compared to manually operated motor or hydraulic shears. For the automation specialists at cts GmbH, the robot is a first step in the development of innovative total solutions for automated pulp handling from the incoming material to the pulper or shredder.
Pulp bales are delivered to the processing industry in units of 6 or 8, which are held together with wires running around them. Manual de-wiring of the bale units, which weigh several tons and are often well over two meters high, with hydraulic shears is demanding and power-consuming, and the highly tensioned wires require great care. The previous, classically automated solutions for dewiring, on the other hand, are often inflexible.
Robotic solution increases safety, efficiency and productivity
With the DWR-U, cts GmbH now presents a robust robotic solution that processes all standard market sizes through special mechanical design without the otherwise usual complex pre-programming.
The system, which weighs around three tons, processes bale units up to 1.8 meters length, 1.0 meters width and 2.3 meters height at a conveying height of between 0.8 and 1.2 meters. The flexibilty of the 6-axis industrial robot allows up to 28 bale units per hour to be de-wired for further processing and their pulp bales to be separated on one or two parallel conveyor lines – around the clock, 365 days a year. The robotic-based design also allows customization for 2 or more lines when using an additional traversing axis. Sensors on the gripper unit ensure reliable differentiation and separation of the wiring of the unit and the rewired individual bales. Cut wires are drawn in by the winding unit belonging to the system and rolled up into a tiny, compact coil.
With a connected load of just five kilowatts, the robot operates very economically. Important for the industry: pulp is sensitive and contamination, for example by oil, could render the bales of an entire unit unusable. With its purely electric drive, the robot manages without the use of liquids.
The system is expandable: In a fully automatic line, companies can transfer the bales of the de-wired unit to a second cts de-wiring robot for automatic de-wiring of single bales. This solution can also be combined with the cts winding system for the wires.
Fast, space-saving and flexible to use
Since neither pneumatics nor hydraulics are used, but instead purely electromechanical drives, the DWR-U requires only a small footprint overall. The system is highly standardized. Commissioning and secure anchoring are uncomplicated and also make it possible to retrofit the dewiring robot for the modernization of existing lines.
“With our fully automated dewiring solutions for pulp unit and bale handling, we have made an extremely successful entry into this market,” says Peter Mackinger, Head of Software Engineering at cts GmbH. “With the automation of pulp handling via standardized robots, we offer unprecedented flexibility in the incoming material area. We will continue on this path. Before the end of this year, cts will present a smart and trend-setting overall solution. Industrial companies or their plant engineers will be able to obtain everything from cts for the fully automated feeding of pulp bales to the converting process.”