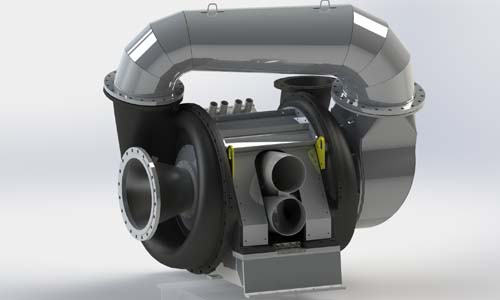
Runtech Systems delivers a vacuum system rebuild to Asaleo Care, New Zealand. Old multistage blower will be replaced with new speed controlled Turbo Blower. The delivery includes an EP600 Turbo Blower with ABB frequency converter, low vacuum blower for wire section vacuums, EcoDrop water separator and EcoFlow dewatering measurement for press suction roll save-all and felt uhle box. With the new vacuum system, Asaleo Care will be able to lower their energy consumption significantly.
“This is an exciting project for our site. Our existing vacuum system is oversized for the current demand and has reached the end of its life. This new system will operate at less than 40% of the existing power consumption, which provides an attractive payback on the investment. With the project in the early stages, Runtech has been professional to deal with and the support documentation provided to date is of a high quality. Despite these challenging times with restricted travel, I’m confident we can work together with Runtech to deliver this project successfully,” says Matthew Bain, Project Manager, Asaleo Care.
“Runtech Turbo Blowers are well known all over the world. This Turbo project is first in New Zealand and we are very happy to work together with Asaleo Care to find an optimal solution for their mill,” says Hannu Kääriä, Sales Director, Asia-Pacific, Runtech Systems.
RunEco EP Turbo Blower is a totally water-free solution with heat recovery potential. New EP600 Turbo is single-stage speed-controlled blower. With integrated high-speed motor controlled by an ABB frequency converter, rotation speed and vacuum level can be adjusted according to the process requirements. Its compact design makes it ideal for rebuilds and also reduces installation costs.
EcoFlow dewatering measurement are designed to measure water flows online accurately and are not sensitive to entrained air or foaming. Measuring dewatering rate enables vacuum level optimization, resulting in maximized sheet dryness after the press section.