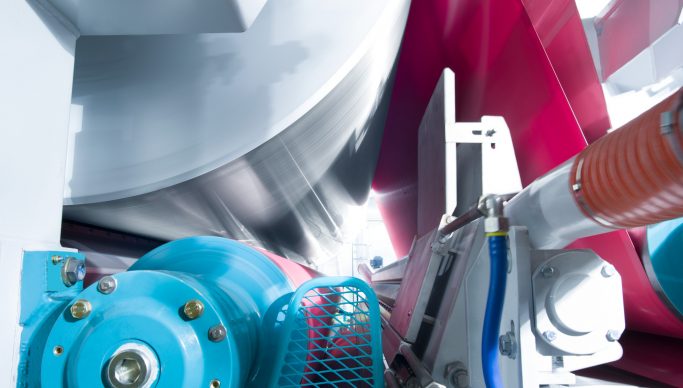
In board machines, threading the paper web following shutdowns or breaks in the dryer section has until now been a complicated and time-consuming process. The process of using ropes to guide the tail through the dryer section presents safety risks and involves an extensive maintenance effort. A new Voith solution offers paper manufacturers unprecedented flexibility and reliability. The TailStabilizer can now be used for the first time in board machines with two-tier dryer sections for ropeless threading of the tail, improving both efficiency and safety. The system is being used successfully at a paper mill in China, for example.
“The fact that we are now able to offer ropeless threading to paper manufacturers that produce grades with particularly high basis weights in two-tier dryer sections is an important milestone for us and is unparalleled in the industry,” says Sebastian Meuthen, Product & Service Manager Paper Machine at Voith. “The system is extremely reliable and, in particular, improves safety for the operating personnel.”
Due to the much higher basis weights in the board segment, ropeless threading is particularly challenging from a technical standpoint. The Voith TailStabilizer system enables absolutely reliable, fully automated and safe threading in the two-tier dryer section. A specially developed peel-up component, positioned as close as possible to the roll, ensures maximum
peeling effect. The optimized arrangement of multi-row air nozzles and air deflectors lifts the tail from the drying cylinders and quickly fixes it to the TailStabilizer to transport it from there to the next drying cylinder. As a result, the process also minimizes shredding. Because it works contactlessly, unlike other solutions, it also avoids wear and unnecessary maintenance work. This results in reduced maintenance and greater equipment availability.
TailStabilizer is part of the Voith Prevo range of tail threading and cutting systems. The threading solution can be adapted for any application and is easy to install. Thus, the system is especially suitable for rebuilds and optimization of existing threading systems. Thanks to its flexibility, the TailStabilizer technology offers a large operating window with basis weights of up to 300 g/m2.