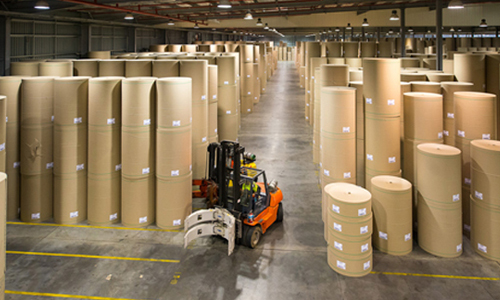
Valmet and Orora Limited have signed a multi-year Mill Maintenance Outsourcing (MMO) agreement to continue taking care of the site maintenance of Orora’s Botany B9 board making line in New South Wales, Australia.
In addition to the MMO agreement, Valmet and Orora have signed a Performance Agreement targeting clear and systematic production and maintenance improvements. Both agreements include Valmet Industrial Internet (VII) solutions to provide a live link between customer and Valmet experts for process optimization. The value of the agreements will not be disclosed. The renewed MMO agreement will be effective as of July 1, 2020.
“Valmet is one of our key performance development partners, supporting B9’s operation and improvement since the start up in 2012. We have worked collaboratively since then with progressive improvements and achievements in key areas such as productivity and cost reduction. This is the second renewal of our MMO and Performance Agreements and we look forward to further success in our cooperation with Valmet. Our objective is to ensure the B9 facility becomes an industry benchmark in all areas of efficiency and cost,” says Craig Nicol, General Manager Operations, Botany Mill.
“We are fully engaged and integrated into the B9 Operations team and have been working side by side to deliver progressive development since the machine’s start-up. The renewal of the MMO agreement is the best acknowledgement for the achievements over the years together with Orora. We’re delighted to be able to share the journey forward with the B9 team and to help continuously optimize the performance of our teams and our equipment and processes,” says Jaegen Peet, Director, Australia and New Zealand region, Valmet.
The long-term relationship further strengthened by Performance Agreement
Valmet has previously supplied the complete B9 containerboard line to Orora, started up in 2012. After the start-up, Valmet took full responsibility of the establishment of maintenance operations, site maintenance services including utilities and management of specific improvement projects.
The ongoing Performance Agreement was renewed for a second time in 2019 with targets and objectives focused on cost outperformance and targeted machine efficiency improvements. The results of the collaboration have been positive considering the previous annual production record was exceeded in 2019 and a new 24-hour production record was set in mid-January 2020.
The Performance Agreement includes access to the Valmet Customer Portal, that will provide an interface for both parties to easily and quickly access visualized data and VII solutions. Although Valmet’s remote services have been utilized since the machine’s start-up, the Valmet Performance Center will now offer the customer a new channel to reach Valmet’s specialists for remote support and case studies. The new agreement also includes comprehensive and expanded automation services.