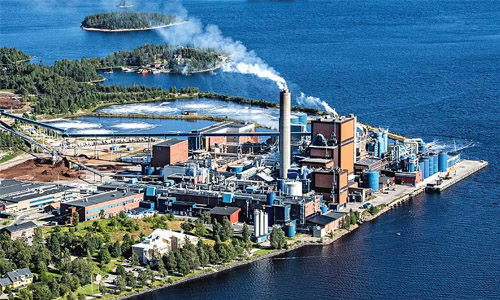
BillerudKorsnäs and SKF are partnering to reduce maintenance costs and improve production output and sustainability performance at Karlsborg Mill in Kalix, Sweden.
Real time data from a new system with 480 connected condition monitoring points at Karlsborg willl be analyzed at SKF’s Rotating Equipment Performance Center in Gothenburg. Combined with a new, performance-based business model, smarter and faster decisions can be made by the mill’s operators and SKF’s engineers, in order to improve Karlsborg mill’s performance.
In addition to improved output, these insights, combined with SKFs knowledge of the rotating shaft and lubrication management will help to reduce the mill’s overall consumption of bearings, seals and lubrication fluids. In doing so, SKF is able to support the mill’s ambitions to minimize the environmental impact of its operations, whilst also reducing costs.
– We are constantly working to improve efficiency in our production together with improvements of stability and safety. This is a step forward for Karlsborg and BillerudKorsnäs, says Petra Einarsson, President and CEO, BillerudKorsnäs.
– By working together, we enable faster, better decision making by operators, improving output and helping machines perform as they were designed to. By adopting a performance-based business model, we directly align our interests with those of the customer, helping to improve their performance, whilst reducing the unnecessary waste that results from a transactional business model, says Alrik Danielson, President and CEO, SKF.
Karlsborg Mill produces over 300.000 tonnes per year of packaging and kraft paper.