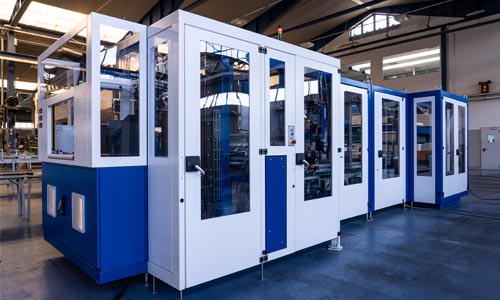
Casmatic B23, an evolution of the best-selling CMB 202, is designed for secondary packaging of roll products such as toilet paper and paper towels. Although it does not replace the primary packaging, the solution creates an outer bag that isolates and preserves the packages, ensuring superior safety during transport and storage. The new model features high performance, a modular design that allows customers to significantly reduce installation time, and sustainability. In this regard, thanks to the TOSS longitudinal sealing system, the Casmatic B23 reduces energy consumption by approximately 20% and pneumatic air consumption by 50%.
Modular design
The Casmatic B23 revolutionises the design of packaging machines by introducing modularity for the first time. This approach reduces installation time at the customer’s site by 45%, marking a true paradigm shift in the industry. In particular, the solution can be installed quickly and easily, allowing production to start in just four days with the support of two technicians. In the future, the aim is to further halve this time and complete the process with just one technician, saving significant resources and time. Capable of producing 23 high quality transparent polyethylene bags per minute, the Casmatic B23 is designed to adapt to a wide range of pack sizes, with an estimated format changeover time of just 25 minutes. This flexibility, much appreciated by customers, increases productivity and enables a quick response to different market needs. So far, customer feedback from field tests of the machine has been very positive due to the simplicity of the format change, which translates into a significant increase in production. Valmet is committed to developing solutions that not only optimise operational efficiency, but also promote the energy transition and contribute to a more responsible and environmentally friendly industrial future.
A Future-Proof Automation System
Another strength is the adoption of Siemens S7 1500 as the standard controller, representing the latest generation of PLCs, ensuring superior operational longevity. This aspect is particularly relevant as the solution is already ready for future technologies, with components and devices that are not expected to become obsolete in the short term. Additionally, the machine, thanks to the proprietary IoT system TDS, is designed to share PLC data through the most widely used protocols available on the market, for integration with a wide range of tools, including third-party ones. This allows for data collection and processing, offering the customer the ability to monitor and optimize machine performance, even in real-time. This feature not only improves efficiency but also enables predictive maintenance functionalities to anticipate potential anomalies and minimize downtime, ensuring greater production continuity and constant monitoring of the plant’s operating conditions. Completing the innovations is the significant improvement of the HMI, now more intuitive and optimized, to facilitate machine use and improve the operator’s experience. This standardized interface not only simplifies daily operations but also contributes to increased customer satisfaction. The first prototype of the solution was successfully installed at an Italian company, which expressed full satisfaction with the machine’s performance.
Cristiano Casale, Valmet’s Global Packaging Technical Director, explains: “Casmatic B23 has been designed with a strong focus on sustainability, even though polyethylene is still the most widely used material in secondary packaging today,” and concludes, “This approach ensures that the machine is ready to meet the growing demand for more environmentally friendly and future-oriented solutions.”
A combination of technological innovation, reduced consumption and modularity, the Casmatic B23 represents an important step towards a more sustainable and digitally integrated future to meet the upcoming challenges of the packaging industry.