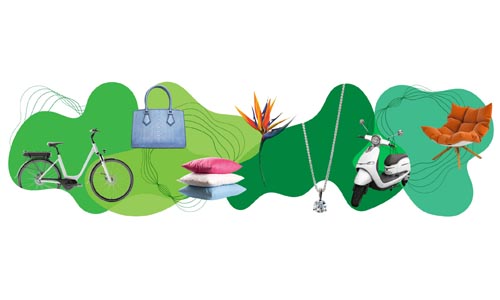
Sappi Europe announced the completion of phase two of a three-phase modernisation project at Gratkorn Mill, Austria. The double-digit million-euro investment consolidates its strong position as a global coated fine paper producer. The objective of this modernisation project is to facilitate future adaptations to meet digitalisation and industry 4.0. The milestone achieved will ensure the risk of machine failure is reduced to an absolute minimum, increasing the production sustainability of the Magno paper range.
Gratkorn Mill is the primary facility of Magno Paper and its flagship location. Magno is a coated woodfree paper, used by customers worldwide for high-end publications, such as art catalogues, books, magazines, annual reports and calendars. This modernisation project underlines Sappi’s commitment to meeting the high demands of the market for quality publications using the Magno paper.
For this phase of the modernisation project, Sappi worked with suppliers such as Honeywell and Siemens to upgrade and increase process visibility and better operator efficiency, leading to more stability in system performance and availability for increased productivity. The upgrade allows processes at Gratkorn to operate on a single automation platform, needing less hardware, cost savings on spares and reduced maintenance services.
“This investment demonstrates Sappi’s belief in the strength and power of printed media & paper-based solutions, driving its constant investment into its production location to secure the portfolio for the long term,” said Rens Huijnen, Product Manager of Sappi Europe.
What’s next
Looking forward, the next phase of modernisation, scheduled for completion in 2025, addresses common challenges in the paper industry, such as sourcing obsolete replacement parts.
“By using state-of-the-art automation and electrical systems, we can not only ensure paper production for our customers at the accustomed high level,” says Dominik Strommer, project manager of the modernisation project, “but also guarantees an easier support by our suppliers.”
Label Papers
Sappi’s Gratkorn Mill has undergone significant development and investment in recent years, showcasing a diverse range of products. Besides graphic papers, the Gratkorn Mill also produces various types of label papers.
In 2021, Sappi expanded its portfolio of wet-glue label papers to include Parade Label Pro (non-wet-strength), ideal for many different applications, such as standard labels for bottles, tins and jars, as well as wrappers for various products.
This was followed by Parade Face SG in January 2022, a high-performance, semi-gloss face stock paper for self-adhesive labels for a wide range of applications – such as food, non-food, beverages, health and beauty care products. Today, this product is also firmly established in the market.
After the ongoing long-term validation phase, in Autumn Sappi Europe will officially launch Parade Label WS, a wet-strength and alkali-resistant wet-glue label paper. Parade Label WS offers excellent printing and finishing results for various applications, including returnable containers in the beverage and food industries.
Sustainability at Sappi Europe
Sappi Europe continues to take strides towards meeting its sustainability and climate commitments. These commitments include enhancing its approach to water stewardship, increasing its share of renewable and clean energy by 11% and reducing total energy by 5%, reducing specific landfilled solid waste by 5% and decreasing specific GHG emissions (Scope 1 and 2) by 25% by 2025.
In line with these ambitions, two investments into renewing the water turbines at Gratkorn Mill’s hydro-electric power plant in 2018-2020 increased its hydro-electric generation by almost 10%. Furthermore, the complete modernisation to shift from a coal boiler to a multi-fuel boiler in 2022, enabled the mill to reduce CO2 emissions by more than 30% as well as sharply reduce dust and nitrous oxide (NOx) emissions. Ongoing projects will further add to these impressive decarbonisation milestones.
All effluent from Gratkorn Mill is oxygen-aerated and fully treated in the waste water treatment plant before it returns to the pure-water river Mur.