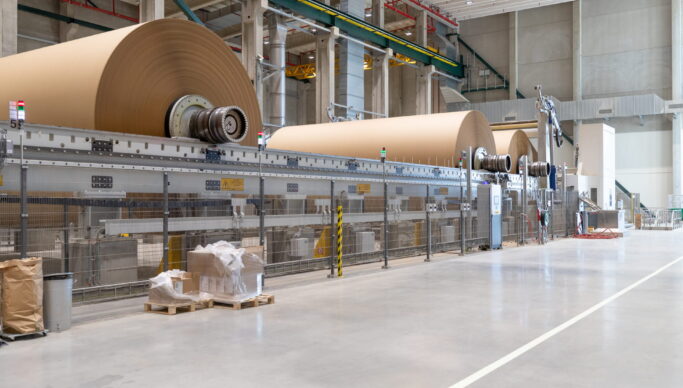
The world’s largest machine for the production of kraftliner is operated by SCA at its Obbola plant in Västerbotten, outside Umeå, eastern Sweden. With a total investment of SEK 7.5 billion, this major project has been completed ahead of schedule and within budget, significantly increasing opportunities to produce packaging materials that replace plastic.
“At full capacity, the machine will increase capacity from 450,000 tonnes to 725,000 tonnes a year, enabling our renewable kraftliner to replace large amounts of plastic and improve the Obbola plant’s competitiveness on the global market,” says Gustaf Nygren, SCA Obbola Plant Director.
The Expansion Obbola investment project has a total budget of SEK 7.5 billion, of which approximately SEK 1 billion has been earmarked for environmental improvements at the site. For example, a biofuel-fired mesa furnace has been installed at the plant with the potential to phase out the use of fossil fuels and save 20,000 tonnes of carbon dioxide emissions.
The new kraftliner machine is manufactured by German global technology company Voith. The total weight of parts delivered to build the 250-metre-long machine reached 11,000 tonnes.
“It’s an impressive machine and a unique project that, despite global geopolitical uncertainty due to the pandemic, war and inflation, was completed faster than planned. It’s a tribute to the organisation of the project and all those involved,” says Gustaf Nygren.
When Obbola reaches full capacity, it is estimated that the machine will produce 725,000 tonnes of kraftliner a year. The path to full capacity requires a new recycled fibre processing unit, which will be housed in the old machine room and will be ready by the summer.
“We then expect a period of adjustment and ramp-up with the aim of reaching full capacity in 2026. At that point, Obbola will be a highly efficient and competitive plant with a product that has the market’s lowest carbon footprint and will be of vital importance for the transition from oil-based packaging material,” says Gustaf Nygren.
In addition to the kraftliner machine, the site’s other premises have also been upgraded with new office space and new skywalks that increase the safety of people at the plant.
Screens for control and monitoring.
A total of around 100 electric car chargers have been installed at the site and some 1,610 cubic metres of wood has been used as building material for the project. This means that the project has stored approximately 1,449 tonnes of carbon in the course of its construction for the long term.
“The kraftliner machine is the heart of this business, which is all about creating renewable material that also generate considerable environmental benefits. We’ve also tried to ensure that forestry’s sustainable raw material is the hallmark of the entire project and I think we’ve done that very well,” says Gustaf Nygren.