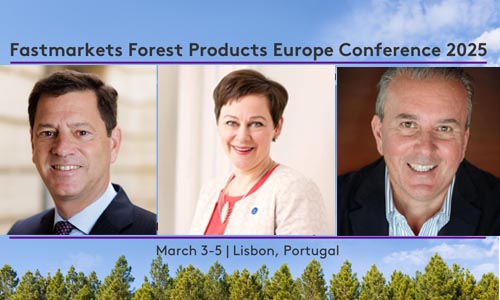
The results are in…
- International CEO of the Year CEO Tony Smurfit Smurfit WestRock
- Woman of the Year Director General Paula Lehtomäki Finnish Forest Industries Federation
- European CEO of the Year CEO Saverio Mayer Smurfit WestRock
Award winners are nominated by a panel of experts, who were particularly impressed by their strategic leadership and their role in positive industry transformation. They will collect their awards at the Fastmarkets Forest Products Europe Conference 2025 in Lisbon on March 3-5.
Throughout the event you’ll enjoy first-rate networking opportunities and meet forest products industry experts like them and get exclusive perspectives on the industry’s most pressing issues like new recycling priorities, shifting trade flows, and the impact of international conflicts.